Expertise
3 min reading
26 April 2022
26 April 2022
Optimal Ways of Ensuring Safety in Manufactories Using Smart Devices
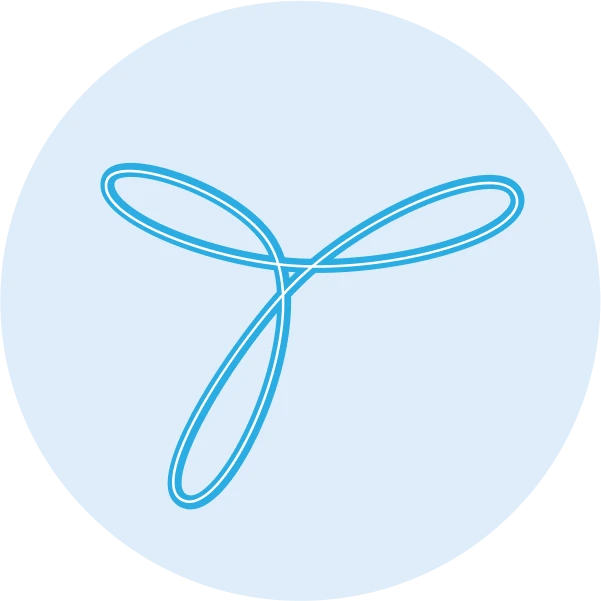
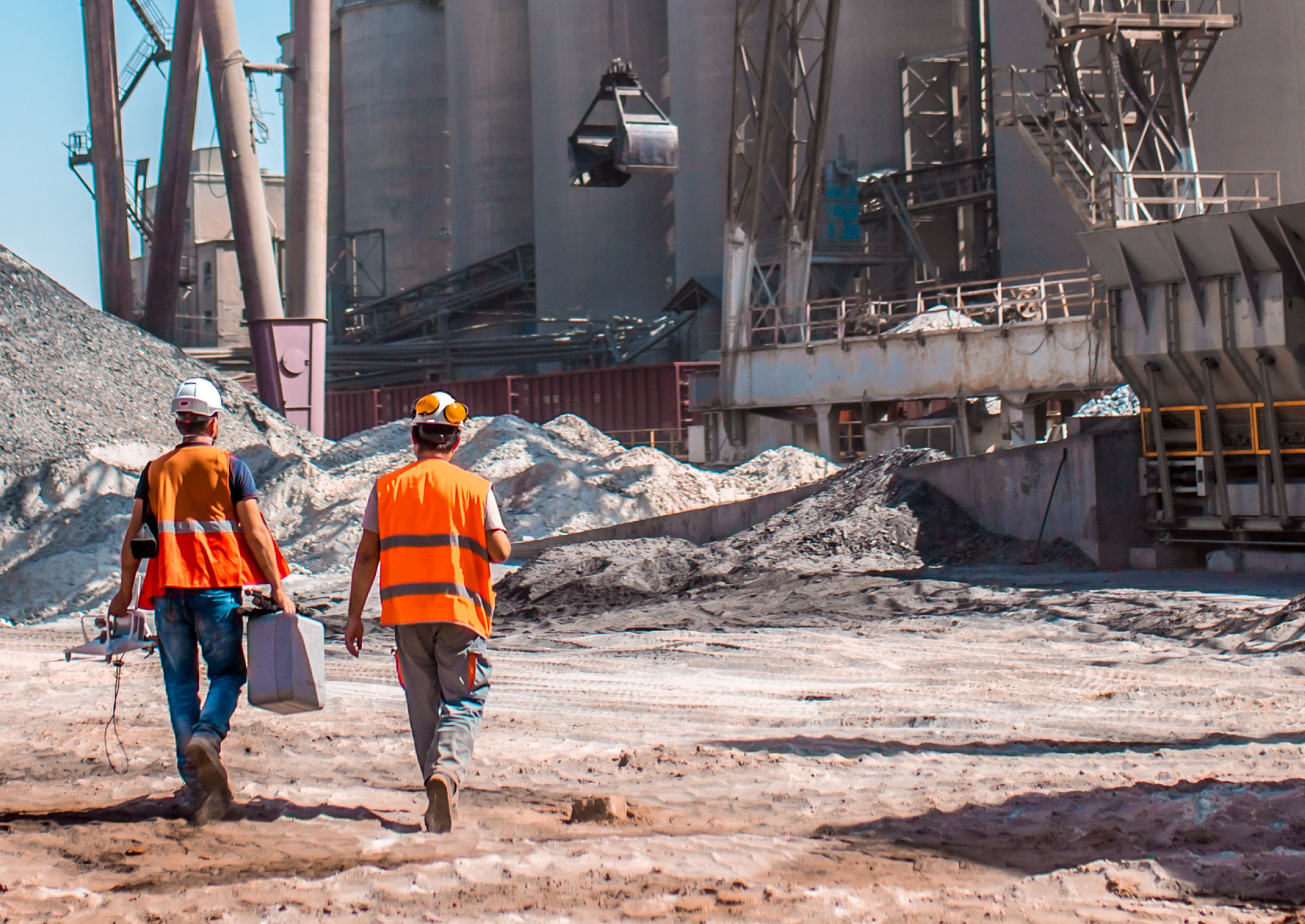
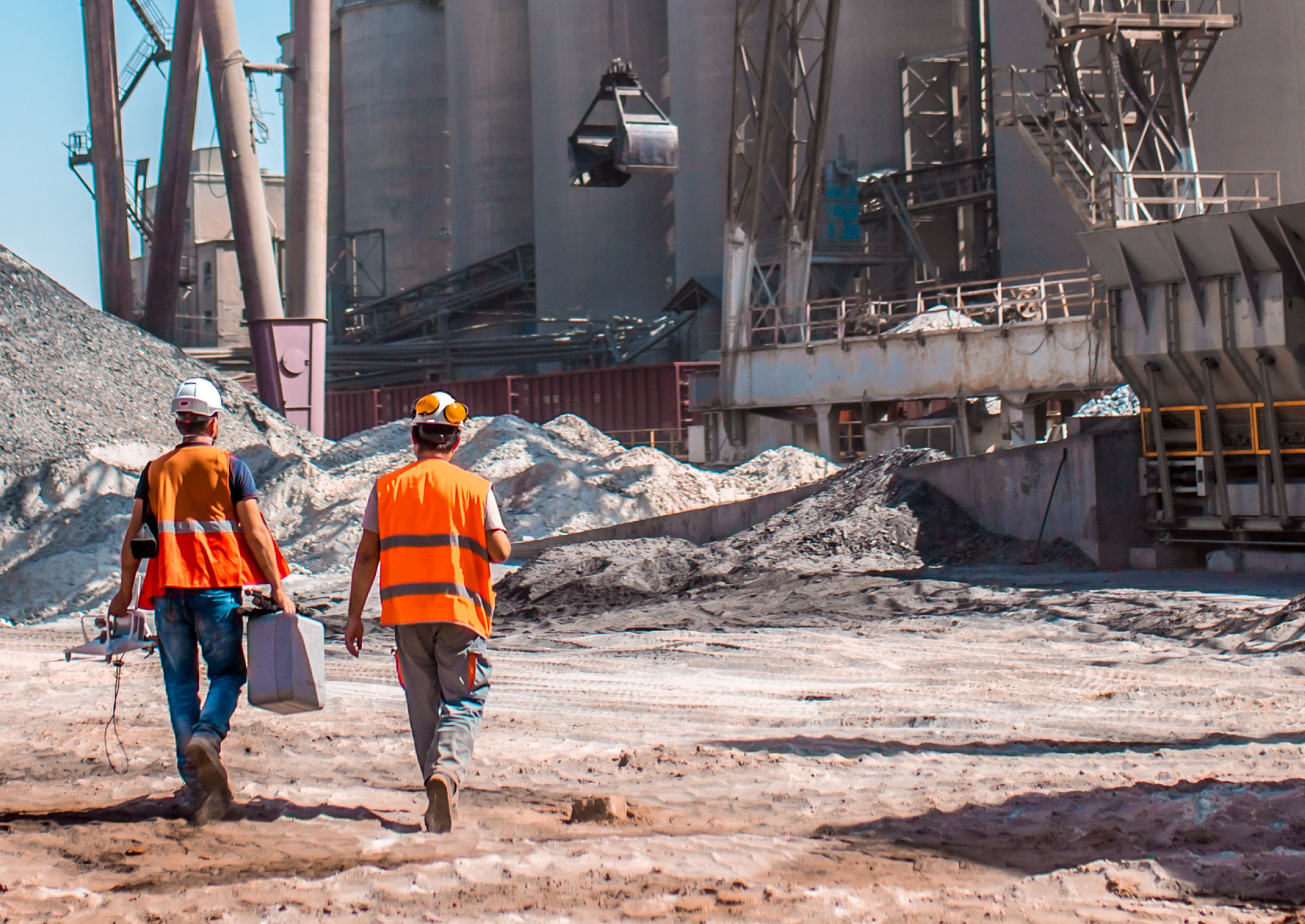
The use of smart devices in manufacturing is one way of making assets safer to operate. The internet-connected devices are equipped with sensors and software that can collect critical data. The information collected can be used to make overall production processes safer. This industrial IoT hardware can be integrated into the work instructions to help workers report any problems that may arise. With the industrial IoT implementation, manufacturing managers can also monitor air quality, noise levels, and ergonomics, which are vital aspects of workplace safety.
Here, you may ask a logical question, “What is industrial IoT?”. In simple words, the Industrial Internet of Things (IIoT) is the platform for connecting physical devices and machines to the Internet in order to collect and share data. The IIoT includes various technologies like big data, industrial control systems (ICS), artificial intelligence (AI), and machine learning. Nowadays, many industrial companies have started using the Internet of Things (IoT) to improve safety. For example, factories can use smart cameras or even some smart home devices to track the location of workers and equipment. This information can be used to reduce the risk of safety issues, unexpected breakdowns, delays, and theft. Additionally, IIoT-enabled devices can be used to monitor conditions that may lead to accidents, such as leaks or spills. By collecting this information, factories can find more advanced ways and take proactive steps to prevent accidents from happening.
Monitoring Possible Risks
One of the main ways of ensuring safety using smart devices is constant monitoring of possible risks. Industrial IoT products enable companies to predict failures and monitor office equipment. This allows one to detect the structural failure of any connected device prior to a tragic accident occurring since security systems will send alerts right to mobile device or PC in advance. The good thing about predictive maintenance is the possibility for organizations to stay informed and make decisions on the basis of data patterns. Predictive maintenance employs machine learning technology to detect possible problems before they affect an employee, company, and more importantly operational performance. Instead of manually analyzing and reporting data, industrial LoRaWAN technology and analytical tools can improve data management efficiency.
IoT solutions for manufacturing can help manufacturers detect flaws in IoT systems long before they strongly affect the enterprise. For example, a smart device can alert personnel via text message to prevent machine failures, or a smart system can be connected to a google home network, so the facility managers will receive necessary updates even at home. With IoT solutions, manufacturers can automate maintenance schedules and improve the overall maintenance capabilities of their appliances. Generally, with easy access to the different sensors and other devices, these solutions will help enterprises extend the life of equipment, reduce employee accidents, and reduce costs associated with employee injuries.
Keeping Track of Employees’ Physical State
In many factories, there is a lot of advanced equipment used, which can put the workers’ lives at risk if they are not careful. One way to improve safety in these conditions is by tracking the employees’ physical state. Industrial IoT trends, in this case, include wearable devices with secure access to data that can connect users and keep track of them using personal identifiers and a digital assistant. There are now various types of wearables that can monitor various aspects of a person’s health, such as their heart rate and blood pressure. The most popular smart device here is a connected watch that monitors heart rate and reminds a worker to take a rest or not enter a dangerous area. These devices are based on simple smart home technology, so they are easy to integrate and use. By wearing IoT devices, employees can be even monitored for signs of stress or fatigue. If a problem is detected, then the employee can be given a break or taken off the job until they have recovered. Besides, a good point about these wearable gadgets is that they can work without Wi-Fi or a cellular network connection.
Another way to track employees is by using smart badges. These badges can be used to track an employee’s location and see if they are following the correct safety procedures. For example, if an employee enters a restricted area, their badge will have denied access. Of course, for this purpose, a factory can use security cameras, smart locks, and a smart front door that allows access only after users check. However, the use of smart badges makes sense since it is much easier for users and controllers as they can disable features of entrance of some badges at any time through remote access. This helps to prevent workers from entering dangerous areas without proper authorization and access given by security managers.
Using advanced technology, such as the industrial IoT, can help businesses improve safety in their factories. By tracking the physical state of employees and using smart devices, companies can ensure that their workers are safe and following the correct security procedures. Enhanced monitoring of company property is able to improve worker safety thanks to health monitoring technologies and wearable technology. Additionally, IoT solutions can be used to identify systems whose failures could cause problems, so management will be able to use this information to make predictions on how to reduce risks and find solutions. Wearable technologies represent a key innovation for IoT applications at work.
Improving Safety Using Analytical Systems
In addition to tracking employee health and location, businesses can also use analytical systems to improve safety in their factories. These systems work pretty much like smart home devices, they collect information from various sources, such as sensors, cameras, and machine data, and then use it to identify trends and problems. For example, an analytical system might be able to detect when a machine is starting to malfunction, identify security issues, and activate security patches if necessary. By detecting a security flaw or any other malfunction early, the company can take steps to fix the problem before it leads to a big accident.
The use of smart IoT devices can help manufacturers solve operational challenges. Using smart secure solutions, manufacturers can easily identify which machines or assets are in use, to which network are they connected, and if they need extra layer protection. Internet of Things devices can also identify any anomalies that occur in the process of production, calculating extra costs, and risks. This information can then be used to make better business decisions. According to the data provided by global companies, with the use of the IoT, factories can increase productivity by up to 15%. On a manufacturing level, this figure is quite significant and can be proof of the prospective future of industrial IoT.
Analytical systems can also be used to monitor employee behavior. For example, if an employee is not following proper safety procedures, the system can flag this and alert management. This helps companies to address safety concerns before they lead to accidents. Overall, analytical systems can be a valuable tool for improving safety in factories. By collecting information from various sources and using it to identify trends, businesses can take steps to fix problems before their actual occurrence.
Increasing the Understanding of Working Environments with the Help of IoT Devices
When employees know how to work, they can reduce the risk of injury significantly. Developing and using IoT devices, and integrating connected sensors is essential to detect a possible threat. Nevertheless, the use of connected sensor systems cannot suffice because it requires an assessment of possible risks which should be dealt with at the best possible time. That is why prior to the integration of IoT monitoring systems at work, employees must understand how they work and how to use them better.
Considering the necessity to understand how exactly connected devices work, it would be advantageous to introduce training courses to staff. Proper training and knowledge can minimize workplace injuries so manufacturers have to provide their workers with this training. AR and VR can be used to simulate complex factory machinery without the associated dangers. Workers just need to connect their VR or AR devices to the internet through a Wi-Fi network or any other type of connection and start learning the operational procedures. Moreover, the data collected from IoT devices can be used to generate highly accurate visualizations that may be later transmitted to smart TVs or other gadgets used for simulation. Consequently, workers can learn specific machinery in a secure environment, so when they face these manufacturing appliances in real life they already know how to use them.
Accelerating the Effectiveness of Rescue Operations
When an accident occurs, it is important to have a quick and effective response. With industrial IoT devices such as a smart thermostat, safety alert system, and GPS tracker, rescue operations can be accelerated. For example, if there is a fire in a factory, the firefighters can use smart devices to get real-time information about the layout of the building and the location of the flames, as well as temperature levels and employees’ location. This information can help them to respond more quickly and effectively to emergencies. Many people are already aware of these technologies since many have similar smart home devices for safety alerts. However, even if you’ve never had a secure smart home device with an Internet connection, it won’t be a problem since IoT devices are really simple in deployment and connection.
Similarly, if there is an injury in a factory, paramedics can use smart devices to get information about the victim’s condition. They can connect to an employee’s wearable even through a guest network or common Wi-Fi networks. By having this information readily available, paramedics can provide better care for the victim, not losing precious time on examining vital signs.
An IoT device can also be used to improve safety during evacuations. By tracking the location of employees, businesses can make sure that everyone is safely evacuated from the building in case of an emergency. Additionally, if there are any employees who are still in the building, their location can be quickly identified so that they can be rescued. When a fatal accident occurs, the rescue operation can be facilitated with IoT devices. It is also possible to create an effective rescue plan for a particular situation with AI.
Overall, the industrial IoT can help to accelerate the effectiveness of rescue operations. By providing real-time information about the location of flames and victims, businesses can respond more quickly and effectively to accidents. This will be helpful in determining the possible threat to employees and production security. IoT platforms can manage and store information to provide a high level of employee safety. IoT tools can be integrated into workforce solutions and HR systems to develop optimal work plans that ensure the worker is properly dispersed throughout 24h.
What are the Possible Challenges of Implementation?
The industrial IoT is a relatively new technology, and there are still some industrial IoT challenges that need to be addressed. One of the main challenges is security. The data collected by smart devices can be sensitive and needs to be protected from cyberattacks. A ransomware attack on smart home devices is much rarer than on industrial facilities, that is why it is necessary for factories to choose a secure router, have a separate network, a reliable password manager that creates complex passwords, and hackers protection against the identity theft. Most people, especially in the business sphere already know that it is dangerous to use default passwords, so they change them to unique passwords immediately after setting up a Wi-Fi router. However, strong passwords are not enough to be 100% protected and it is better to create an unusual name, so hackers won’t be able to resolve it.
Secure smart home starts algorithm is also quite similar to the starting process of the network for the whole manufactury. It is important to set two-factor authentication, and never save passwords, especially when logging in through a different network. Two-factor authentication is one of the best methods to ensure the security of the device, and protect the network from hackers.
Another challenge that may occur when implementing a smart device into your existing network is data interoperability. The various types of data collected by different devices need to be able to work together so that they can be analyzed and used effectively. That is why it is much better to create a network using the devices from one provider as they are already compatible with each other and don’t require additional links to transmit data. When you create an ecosystem with one device provider based on one network protocol, the connection will be more secure and hackers won’t be able to attack it.
How Can TEKTELIC Help Enhancing Safety in Manufacturing?
TEKTELIC Communications has experience in a lot of spheres, including a smart home device area, healthcare, agriculture, and industrial area. Our main focus has always been safety and security, together with people’s well-being. Our manufacturers have developed reliable devices for security purposes within the industrial area.
The main device here is TEKTELIC KONA Strand Macro Gateway. This gateway can operate in extreme temperatures (from -40°C to +60°C) and high humidity (from 5% to 100% condensing), which makes it perfect for a manufacturing environment. This gateway has geolocalization support, so you always know its precise location. It represents a completed connection solution protected from hackers, and compatible with all devices in the LoRaWAN network.
One more device designed for safety improvement is TEKTELIC FINCH. This sensor works like a panic button, so an employee can send an emergency alert any time they feel danger. The panic message is sent together with location data, so the reliable staff will respond to the emergency request shortly. What is more, this device has a battery life of up to 5 years, so this purchase will be a justified investment for an enterprise.
At TEKTELIC, we have a team of experts who can help you to take advantage of the industrial IoT to improve safety in your factory. We can help you to install and configure the necessary sensors and devices, and we can also provide support for data collection and analysis.
Contact us today to learn more about how we can help you to improve safety in your factory.