Expertise
4 min reading
4 October 2022
4 October 2022
How to Improve Efficiency in the Factory with the Internet of Things?
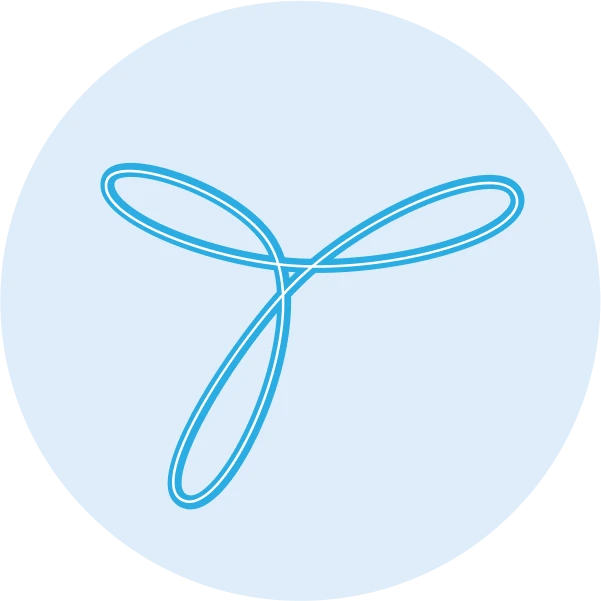
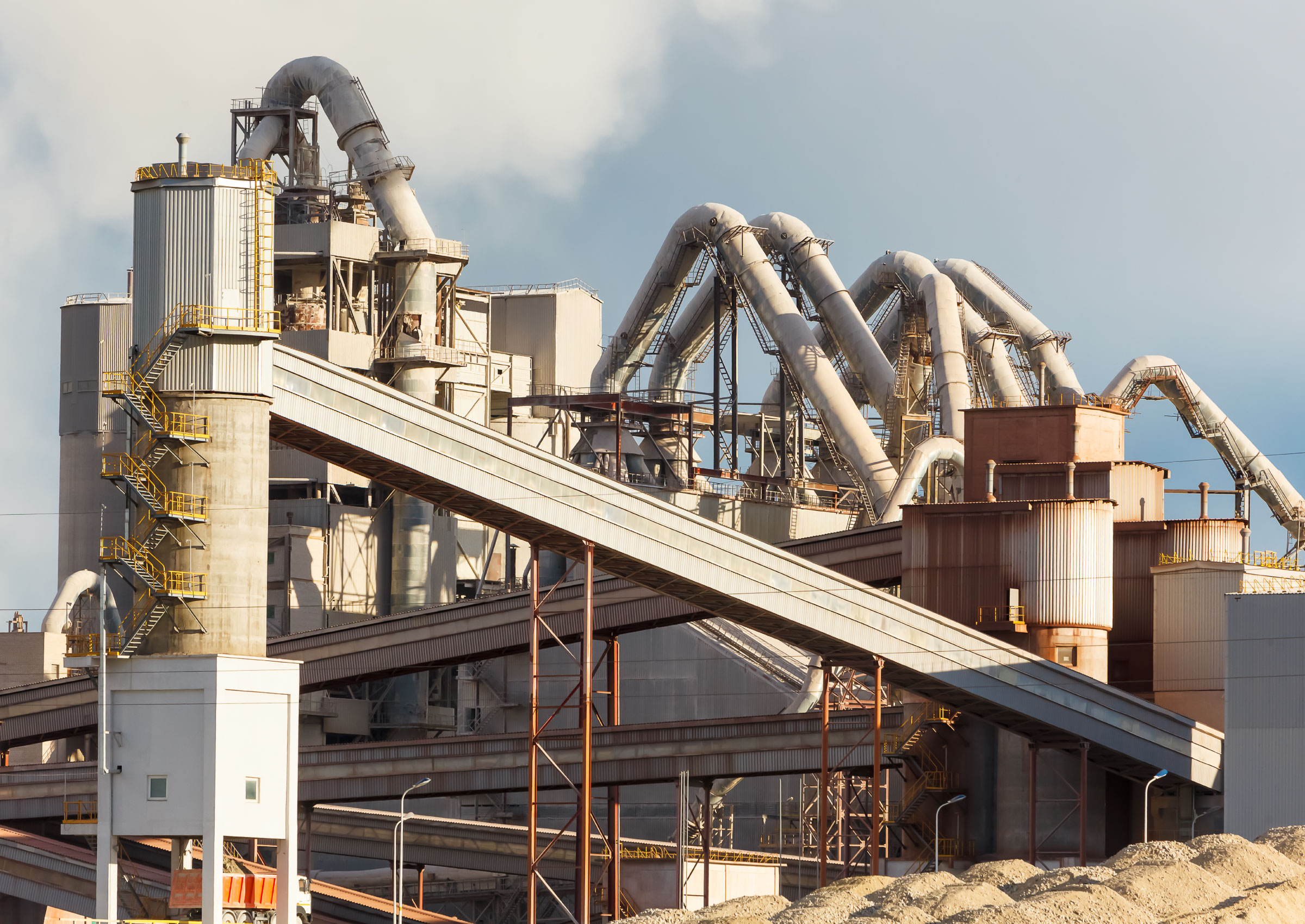
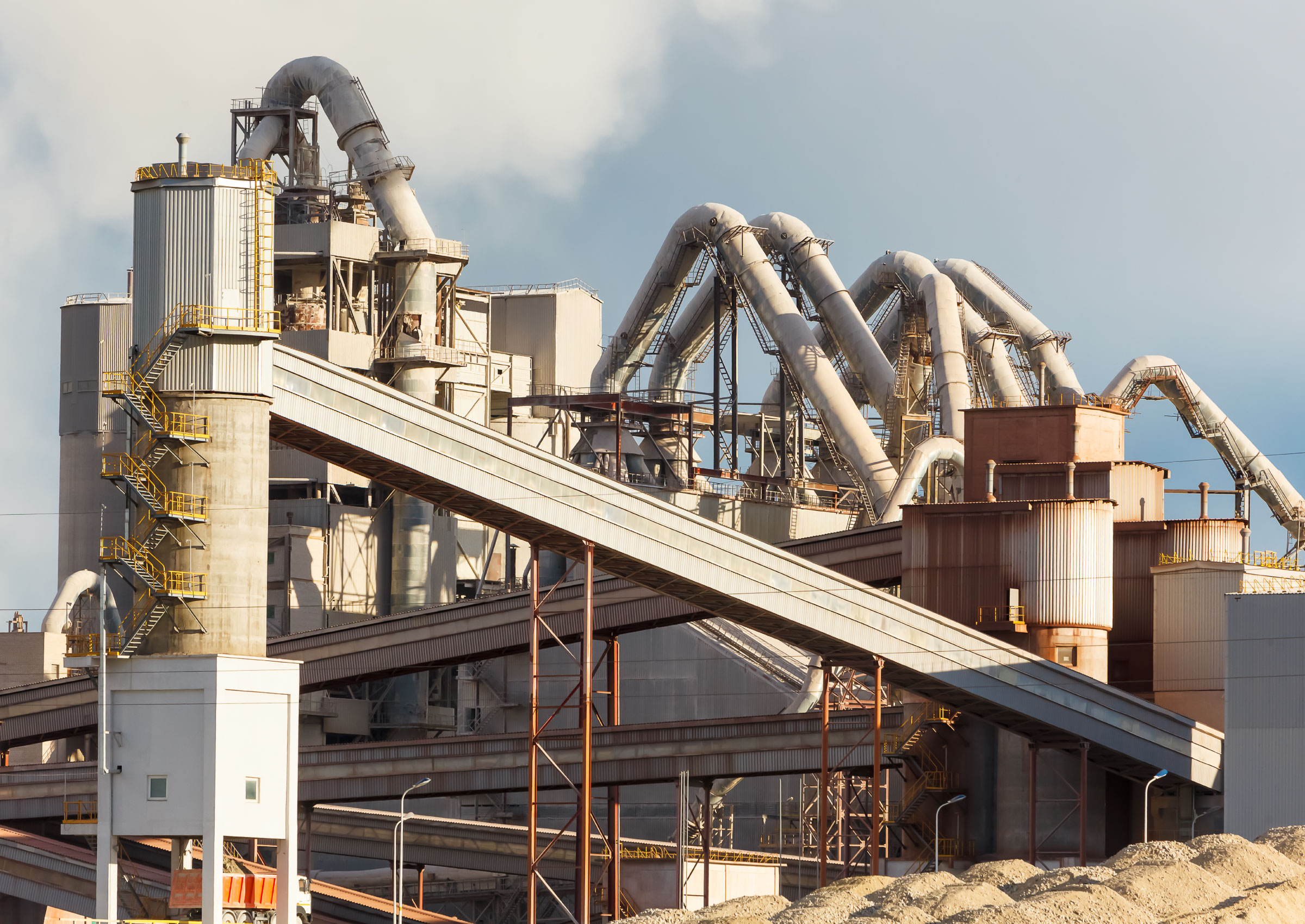
Full-scale training is vitally important for the industrial environment. Production systems, technological development, and manufacturing process efficiency, in general, vary in different places. That is why detailed training and preparation of personnel, especially newbies is a necessity for smooth manufacturing operations. The use of industrial IoT services for the workers’ training, in turn, can bring a bunch of benefits and facilitate the process. The main point here is to understand how to organize this digital training and make it efficient for factory purposes.
Main Steps towards Establishing Machine Learning Models in a Factory
The implementation of industrial IoT platforms for full-scale factory training can lead to improved productivity and better operational efficiencies in a variety of ways. For instance, IoT wearables can collect data on worker activity and environmental conditions. It can also help monitor employee safety and health. Moreover, such industrial IoT devices can help in achieving fully managed service in manufacturing. The integration of the Industrial Internet of Things will change the way factories make products and train their workers. IoT factory automation will help companies make their operations faster and more flexible, and it will increase their bottom line.
The implementation of industrial IoT solutions in a factory will involve implementing several connected devices to monitor production processes and improve supply chains. Networked machines with advanced analytics can provide feedback about real-time production rates, allowing companies to make more informed purchases and effectively organize production operations. Additionally, with the industrial IoT, companies will be able to monitor and adjust their production parameters, reducing the possibility of human error. Considering all the above-mentioned reasons, IoT-connected factories with digital learning are something that is necessary for factory success.
Getting People with the Right Skills
As the adoption of IoT technologies continues to grow, businesses need to ensure that their workforce is prepared to handle this new industrial IoT equipment. To achieve this, companies will need to improve their IT security, data management, networking, and big data analytics capabilities. These new skills will be important for businesses as they make the transition to the Industrial Internet of Things and the fourth industrial revolution. Fortunately, there are a number of ways to get the skilled IoT professionals you need using digital transformation and learning.
Companies must start by refreshing their recruitment strategy. Look for those with relevant skills, who have a passion for learning new technologies and are eager to embrace change rather than for those people who follow old methods and don’t want to accept any technological solutions. This includes recruiting those who can adapt to the ever-changing technology landscape and grow with the company. For manufacturing companies, it also means asking the right questions, making clear the expectations of the role, and offering attractive incentives.
To prepare the workforce for a new, smart factory, manufacturers need to hire workers who already possess the right skills. This means a workforce that understands data science, automation, and soft skills. A workforce that has the proper knowledge and experience can make a huge difference together with seamlessly integrated digital learning. Proper smart manufacturing background will also help them adapt to new trends, cultural expectations, and security procedures in smart factories.
Establishing Cutting Edge Technology
Eliminating bottlenecks in the mechanical engineering process requires a system that monitors and acts on real-time information about the manufacturing process. The smart system helps manufacturers to identify areas of inefficiency before they increase production costs. That is why in order to establish an effective digital learning environment, it is a must to have a reliable IoT system, which connects the physical world and cloud computing.
With the use of the Internet of Things, manufacturers can measure production performance and improve efficiency. Besides, by providing real-time visibility to production status, manufacturers can identify potential bottlenecks early in the process, which can help them create continuous improvement programs that address the problems. It is also much easier to train new workers using existing systems rather than completely new tailored for workers’ training.
Providing Access to Real-Time Data
Real-time data is increasingly important to create models for factory automation IoT training and normal operation of a team further on. This is useful for a variety of reasons, including helping drivers better understand traffic conditions or facilitating analytic projects. In general, industrial IoT applications depend a lot on the data quality and frequency of data acquisition. In case when new workers are trained using old data, the training itself may be ineffective as it will not be relevant for the current standing of manufacturer, and some of the environment can be completely replaced or out of use.
For effective training and data sharing, real-time data has to be easily accessed on a wide variety of devices, including mobile devices. When trainees can access and analyze data visualization from smart sensors or any other manufacturing equipment without additional difficulties by simply using a mobile device or PC, it improves their involvement in training.
Real-time production data collection and analysis can help manufacturers in multiple industries to make better decisions for rapid development and cost reduction. Businesses can make faster decisions, which can lead to higher levels of flexibility and agility in their operations following manufacturing innovation. Collecting data points in real-time and exchanging them will advance manufacturers to the top industrial IoT companies and improve manufacturing processes. Such data gathered can also provide better service to stakeholders as they’ll be involved all the time in the operational processes knowing that everything is transparent and made for consistent rather than rapid growth. With access to real-time raw data, they can better understand how to improve their processes.
Giving Real Equipment to Use
Giving trainees real equipment is crucial for effective manufactory training. In manufacturing, training employees is critical to the success of an organization and they need to know how exactly the process and manufacturing devices work. This type of training provides workers with the knowledge and skills to succeed in a variety of roles, using and analyzing data on-site. Such a training approach also improves a workforce’s output and innovation potential of the workers. Using a variety of learning modalities and real manufacturing equipment in training can elevate the experience for employees and raise the level of training in general. For example, eLearning modules can help employees review safety training only if they involve the actual devices for remote monitoring of employees.
For example, TEKTELIC SEAL can be a perfect choice for such training purposes on security tools usage as it is actually can be used in the real industrial environment for worker tracking. SEAL is GPS and BLE enabled, so it works equally well inside and outside the manufacturing premises. It has an operable temperature range of -20°C to +50°C and long battery life of up to 6-12 months without the need to recharge. The device data is sent via LoRaWAN, making this IoT device positive for the energy efficiency of the factory.
Another useful and effective device to be involved in training and manufacturing is ORCA, which is designed specifically for industrial asset management and is streaming data via LoRaWAN as well, which makes it an energy-efficient and beneficial choice. ORCA has 5 years of battery life, operating in the extreme temperature range of -40°C to +85°C. It locates assets in the field with the GPS and optional BLE technology, so ORCA can sensor data and transmit it to the end-user right away regardless of the availability of direct connection with the sky.
Ensuring the Secure Network Connection and Cloud Architecture
A secure IoT network that protects trainees and the company against data leaks and hackers is a crucial component for smooth and risk-free integration of the factory to industry 4.0. IoT projects generally can only be successful when are reliable and secure. There are many network options in the market today but not all of them are well-encrypted and trustworthy. Wi-FI can be hacked quite easily while some more narrow technology like Helium, still have difficulties with signing to the network. LoRaWAN, in turn, is free of the abovementioned risks and controversy so far. It is a highly secure network as within a network data packages are sent to the devices and end-users encrypted and even if received by the wrong device cannot be decrypted that easily.
Moreover, it is also crucially important to have a gateway, which connects the sensors to cloud computing and transfers IoT data. The gateway should also pre-process data before transferring it to the cloud applications. For this purpose, TEKTELIC industrial gateways are your ideal choice. KONA Enterprise Gateway, for instance, is a cost-effective gateway made for enterprise deployments, which has LoRaWAN, 3G/4G, and GPS antennas for connection flexibility. It uploads remote software updates and with an MTBF of 50 years, it is “always on” with the lowest TCO from the operator. The mounting options are diverse, so you can attach it to a pole, wall, or tower building DIN rail. It is created for outdoor deployments, so the enclosure is highly resistant and suitable for the manufacturing facility.
What are the Possible Challenges?
Despite the advantages of IoT industrial training, it is important to understand the risks associated with the technology and training.
Scaling
One of the biggest challenges is scaling. The implementation of IoT systems is sometimes complex for people, who do not understand the technology well. As a result, a lot of companies fail to scale their projects past the proof of concept phase. So, it is critical to choose a vendor that offers end-to-end support and training for its clients. The organization must also ensure that its IoT devices can be updated automatically and efficiently.
Lack of Knowledge
Among the other challenges, we can name a lack of knowledge about the technology. In an increasingly digital world, the Internet of Things is transforming everything we do and creating new jobs together with new approaches to raw materials. While the IoT will create efficiencies, it will also require workers to understand the new technology. This means that companies need to ensure that they have the right skills for IoT training, using telemetry data, and web apps.
That is why it would be a smart decision to choose workers, who underwent graduate programs specializing in IoT. These programs focus on the full lifecycle of product development and end-user use of IoT devices. They also explore the business impact of IoT and help participants become more effective in their careers. So, these people already know how device management works and how it influences product quality.
Lack of Consistency
Most training programs focus on problem-solving skills and techniques that are easy to teach, but they don’t focus on how to find the root cause of a problem. At the same time, proper manufacturing training requires disciplined thinking and close attention to detail. It also requires employees to ask themselves, “How do we know that?” and to look beyond the most obvious “symptoms” to determine the underlying cause. Without this, organizations will remain prisoners of basic courses without much value.
So, to make these pieces of training consistent, it’s necessary for companies to pay attention to details and include relevant real-time data. Real-time data can also help companies teach newbies how to monitor incoming orders and product availability. They can then take quick action to increase supplies or find short-term contract labor. Real-time data can also provide insight into errors and prevent them from affecting the business. Ultimately, real-time data can prevent costly errors that can slow down operations.
Benefits of Smart Training for Manufacturing Workers
The benefits of IoT in manufacturing training are numerous, especially for those workers involved in the public sector and service-related environments. For example, IoT can help businesses monitor their inventory, improve the quality of their products, and manage their supply chain, which are crucial things to know for the workers. This way, the workers can react accordingly and deploy resources in order to repair the situation.
By reducing waste and improving efficiency, manufacturers can reduce their production costs while improving employee satisfaction and knowledge necessary for manufacturing. Eliminating bottlenecks is an essential part of these practices as well and IoT data gathered and analyzed by both people and artificial intelligence can help increase the productivity of the company. Manufacturers should analyze their entire value stream to find out where they are experiencing inefficiencies and digital training is useful for this.
Summing up
As manufacturing becomes smarter, the demand for qualified data scientists and specialists will increase. Without enough skilled professionals, industry executives will struggle to make informed decisions, which will work for smart cities and technologically-advanced environments. As a result, educational training for these professionals should be implemented as quickly as possible. It’s essential that manufacturers understand the value of IoT in manufacturing and start investing in their future workforce.
Developing an IoT-enabled factory can help you achieve smarter manufacturing processes and better end results. Using IoT technology in training can also help you create products faster and more efficiently. Companies need to integrate operations and departments into it to get the most out of the IoT benefits. So if you want to convert your manufacturing training or the workflow into a smart one, or simply understand what is industrial IoT and how to apply it to your factory, don’t hesitate to contact the TEKTELIC sales team, they’ll be happy to answer all of your questions.